Staff shortages in logistics – is automated inventory management the answer?
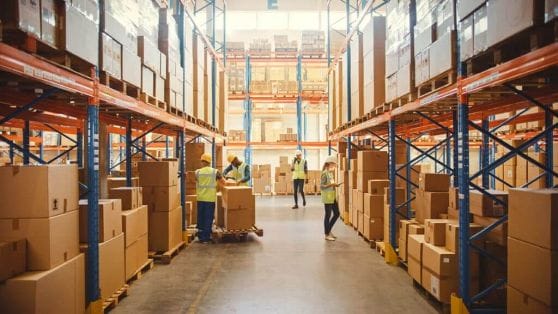
The logistics industry has taken a huge hit when it comes to staffing and recruitment over the last three years, with natural attrition being exacerbated by Brexit and COVID.
Initially that largely hit HGV drivers, but soon spread to include more general warehouse staff – 13% reported severe warehouse staff shortages, and 24.5% said they were struggling to get van drivers (Logistics UK’s September Performance Tracker 2022). Just 12 months earlier, there were no shortages of either.
ONS data, meanwhile, points to a doubling of online job adverts for transport, logistics and warehouse positions compared to the previous year.
Fewer staff means higher bills
There might be fewer workers out there ready to fill warehousing jobs, but the demands from the consumer has never been higher. Next day – or even same-day – delivery is now the expectation, putting greater pressure on 3PLs to not only deliver products faster, but also to keep on top of their stock in a much faster moving landscape.
This means the staff that are available can command higher wages, especially at peak times of year – warehouses in Britain were paying up to 30% more to recruit staff to cope with Black Friday and the Christmas run-in.
The warehouse trade group and an industry recruitment agency, meanwhile, reported that they were struggling to replace the European staff who used to travel to the UK during those periods to augment the UK-based workforce.
The impact isn’t just being felt at peak times of year, either. Clare Bottle, CEO of the UK Warehousing Association, said pay being offered for entry level jobs had risen between 20-30% – and said the industry was ‘tens of thousands short’ when it came to staff numbers.
Specialist recruiter Jordan Francis, commercial director of the Prodrive recruitment agency, has recently had to offer a 25% pay increase to help fill a huge number of vacancies. While that not only costs the warehouses considerably more, it has also meant workers are less likely to work overtime.
Staff impact
These shortages are impacting warehouse workers in several ways. The extra demand not only means stress levels are increasing, but also increase safety risks as staff try to do more, with less.
Morale is suffering too, with warehouse workers all too aware that newer recruits with less experience will have been offered more money to entice them into the job.
Why it matters to others
Staff shortages in warehouses have very real implications for the public and retailers too. With fewer staff available to sort and dispatch products, retailers may have to return to the days when delivery times were upwards of five days.
At best, these items are luxuries that the consumer will simply try to find elsewhere (albeit from a competitor). At worst, these are critical items that the consumer is being forced to wait for because there’s no other option.
Other items may cease to be offered online at all. If a retailer is selling items with a smaller margin, these may not be cost-effective to sell online if the increased staff costs wipes that low margin out completely. While we’ve only had online shopping with this level of speed and ease for a few years, it would still feel like a real step backwards if shops had to cut items for sale and increase delivery times.
Automated inventory management could help
We’re increasingly hearing from potential customers that the staff losses are a key driver for them when it comes to investigating and implementing automation.
When most think about automation in the warehouse, they think of drones picking and carrying parcels – but that’s just the tip of the iceberg. Our fleet of automation units is able to take the strain on many tasks – from inventory and stocktakes from the minute pallets enter the warehouse, through to the streamlined movement and loading of pallets.
These robot solutions can be implemented without any major impact on your warehouse infrastructure (unlike traditional drone solutions which require long installation periods and involve shutting down sections of the warehouse).
When it comes to solutions like inventAIRy XL, the ROI can be demonstrated with a proof of concept that takes just 24 hours, meaning warehouse managers can go from initial enquiry through to automated inventory management in an incredibly short timeframe.
Once implemented, our solutions can take the strain off your staff and allow them to focus on the jobs that can’t be automated. On top of that, it will increase warehouse efficiency and accuracy, giving 3PLs a real edge when it comes to winning new business.
If you want to see how automated inventory management or pallet movement could transform your warehouse, email us or give us a call on 0203 488 4071.
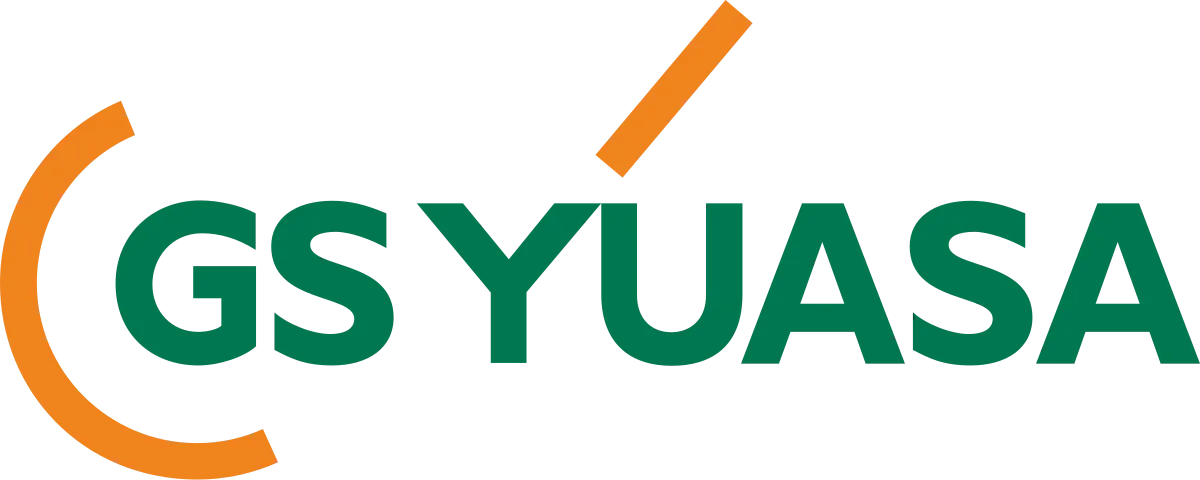
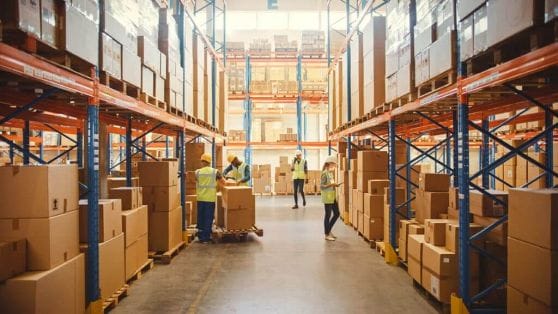
The logistics industry has taken a huge hit when it comes to staffing and recruitment over the last three years, with natural attrition being exacerbated by Brexit and COVID.
Initially that largely hit HGV drivers, but soon spread to include more general warehouse staff – 13% reported severe warehouse staff shortages, and 24.5% said they were struggling to get van drivers (Logistics UK’s September Performance Tracker 2022). Just 12 months earlier, there were no shortages of either.
ONS data, meanwhile, points to a doubling of online job adverts for transport, logistics and warehouse positions compared to the previous year.
Fewer staff means higher bills
There might be fewer workers out there ready to fill warehousing jobs, but the demands from the consumer has never been higher. Next day – or even same-day – delivery is now the expectation, putting greater pressure on 3PLs to not only deliver products faster, but also to keep on top of their stock in a much faster moving landscape.
This means the staff that are available can command higher wages, especially at peak times of year – warehouses in Britain were paying up to 30% more to recruit staff to cope with Black Friday and the Christmas run-in.
The warehouse trade group and an industry recruitment agency, meanwhile, reported that they were struggling to replace the European staff who used to travel to the UK during those periods to augment the UK-based workforce.
The impact isn’t just being felt at peak times of year, either. Clare Bottle, CEO of the UK Warehousing Association, said pay being offered for entry level jobs had risen between 20-30% – and said the industry was ‘tens of thousands short’ when it came to staff numbers.
Specialist recruiter Jordan Francis, commercial director of the Prodrive recruitment agency, has recently had to offer a 25% pay increase to help fill a huge number of vacancies. While that not only costs the warehouses considerably more, it has also meant workers are less likely to work overtime.
Staff impact
These shortages are impacting warehouse workers in several ways. The extra demand not only means stress levels are increasing, but also increase safety risks as staff try to do more, with less.
Morale is suffering too, with warehouse workers all too aware that newer recruits with less experience will have been offered more money to entice them into the job.
Why it matters to others
Staff shortages in warehouses have very real implications for the public and retailers too. With fewer staff available to sort and dispatch products, retailers may have to return to the days when delivery times were upwards of five days.
At best, these items are luxuries that the consumer will simply try to find elsewhere (albeit from a competitor). At worst, these are critical items that the consumer is being forced to wait for because there’s no other option.
Other items may cease to be offered online at all. If a retailer is selling items with a smaller margin, these may not be cost-effective to sell online if the increased staff costs wipes that low margin out completely. While we’ve only had online shopping with this level of speed and ease for a few years, it would still feel like a real step backwards if shops had to cut items for sale and increase delivery times.
Automated inventory management could help
We’re increasingly hearing from potential customers that the staff losses are a key driver for them when it comes to investigating and implementing automation.
When most think about automation in the warehouse, they think of drones picking and carrying parcels – but that’s just the tip of the iceberg. Our fleet of automation units is able to take the strain on many tasks – from inventory and stocktakes from the minute pallets enter the warehouse, through to the streamlined movement and loading of pallets.
These robot solutions can be implemented without any major impact on your warehouse infrastructure (unlike traditional drone solutions which require long installation periods and involve shutting down sections of the warehouse).
When it comes to solutions like inventAIRy XL, the ROI can be demonstrated with a proof of concept that takes just 24 hours, meaning warehouse managers can go from initial enquiry through to automated inventory management in an incredibly short timeframe.
Once implemented, our solutions can take the strain off your staff and allow them to focus on the jobs that can’t be automated. On top of that, it will increase warehouse efficiency and accuracy, giving 3PLs a real edge when it comes to winning new business.
If you want to see how automated inventory management or pallet movement could transform your warehouse, email us or give us a call on 0203 488 4071.