GS Yuasa Transforms Year-End Stock Audit with inventAIRy XL
Overview
GS Yuasa is a globally recognised manufacturer of automotive and industrial batteries, with a long-standing reputation for engineering excellence and operational reliability. Their UK Distribution Centre in Swindon plays a pivotal role in the storage and distribution of batteries to customers across the UK and Europe.
Like many high-volume distribution centres, GS Yuasa places a premium on inventory accuracy – ensuring the right product is available at the right time. Historically, their approach to full wall-to-wall inventory audits, though rigorous, posed logistical and operational challenges. In 2024, GS Yuasa partnered with RAWview to deploy the inventAIRy XL solution – a cutting-edge autonomous drone system designed to perform high-density warehouse audits quickly, safely, and with minimal disruption.
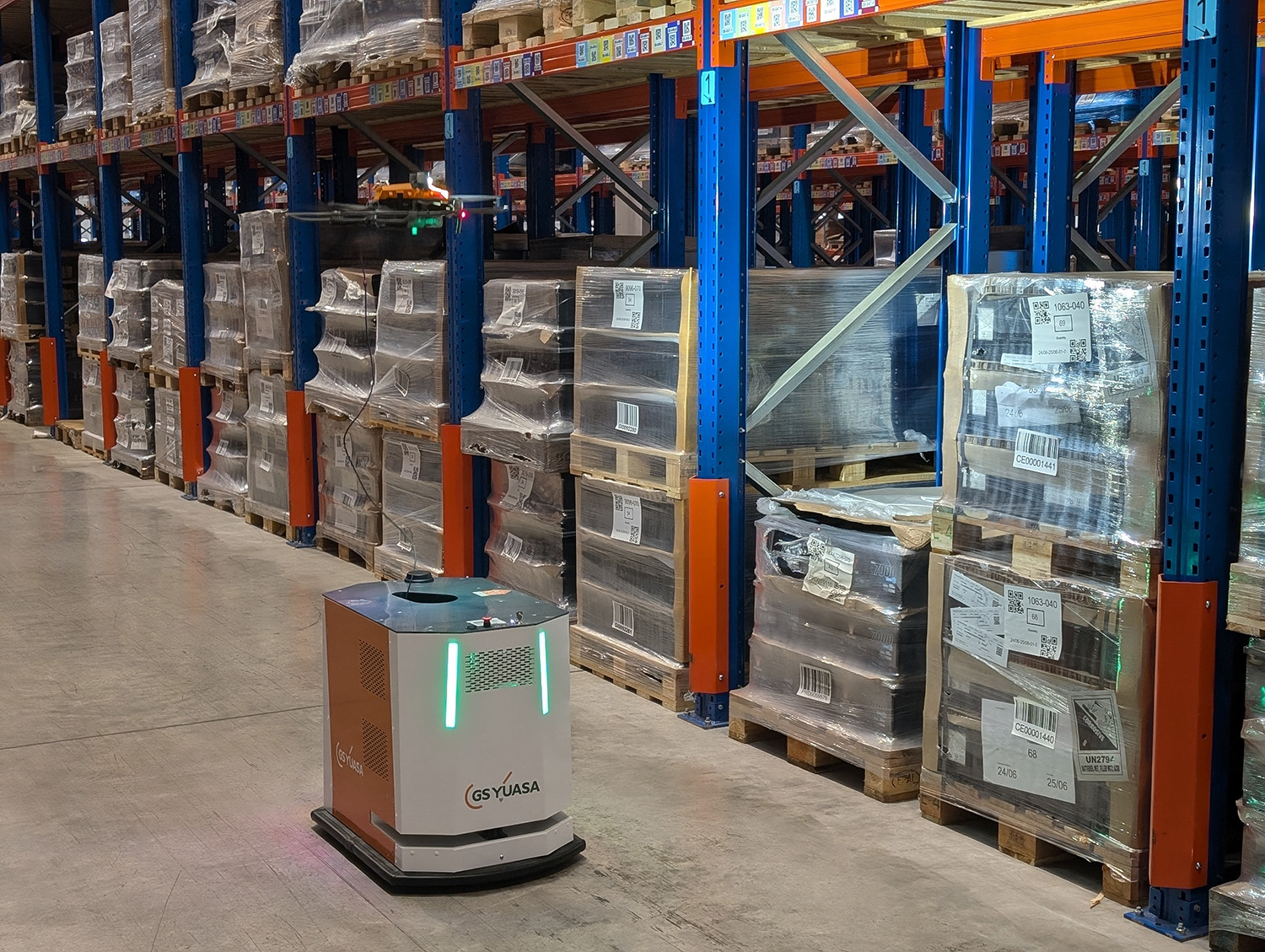
The Challenge
Prior to the introduction of inventAIRy XL, GS Yuasa’s annual inventory audit required a complete site shutdown for three days, during which all warehouse operations were paused. This approach came with a series of drawbacks:
- Significant downtime: A multi-day pause in operations affected inbound and outbound logistics, introducing bottlenecks and delays.
- High temporary labour demand: The audit required a large number of staff to work extended shifts, often on overtime rates, to ensure the task was completed on time.
- Equipment hire and safety concerns: Scissor lifts and manual barcode scanners were used to reach high-bay pallet locations, introducing safety risks and significant rental costs.
- Data lag: Inventory data could only be validated and reconciled once the audit was fully complete, delaying insights and corrective actions.
In short, the existing audit process was costly, disruptive, and resource-intensive.
The Solution: inventAIRy XL
To overcome these challenges, GS Yuasa implemented three inventAIRy XL systems across their Swindon facility.
inventAIRy XL is an autonomous inventory solution that combines a mobile robot, tethered drone, and AI-driven image capture system to automate stocktaking. It seamlessly navigates aisles, scans barcodes across all rack levels (including high bays), and automatically uploads inventory data to a secure user interface – eliminating the need for manual scanning and related equipment.
For GS Yuasa, the system was deployed to perform a full wall-to-wall audit of approximately 25,000 pallet locations, without interrupting their day-to-day operations.
The Outcome
The deployment proved to be a transformative success:
- Full audit completed in just 18 hours: The entire count was conducted overnight, with all three drones working in parallel to autonomously scan the warehouse – a fraction of the time previously required.
- Zero operational downtime: Unlike previous years, the audit required no site shutdown. Normal operations resumed immediately the following morning.
- Improved safety and reduced cost: The solution removed the need for temporary scissor-lift hire and greatly reduced the requirement for manual labour and overtime shifts.
- Real-time visibility: Inventory data was processed and available through the inventAIRy XL dashboard in real-time, giving GS Yuasa’s stock control team near-instant insights into their inventory accuracy.
- Scalable success: The use of three systems allowed for rapid coverage across all zones, demonstrating the potential to scale the approach to other sites or repeat the process more frequently.
Client Impact
This deployment marked a major shift in how GS Yuasa approaches inventory assurance. Not only did the inventAIRy XL solution deliver immediate operational efficiencies, but it also aligned with the company’s broader goals around digitisation, sustainability, and continuous improvement.
By reducing the need for powered access equipment, the audit also contributed to improved health and safety outcomes for staff and reduced emissions linked to equipment charging and extended operating hours.
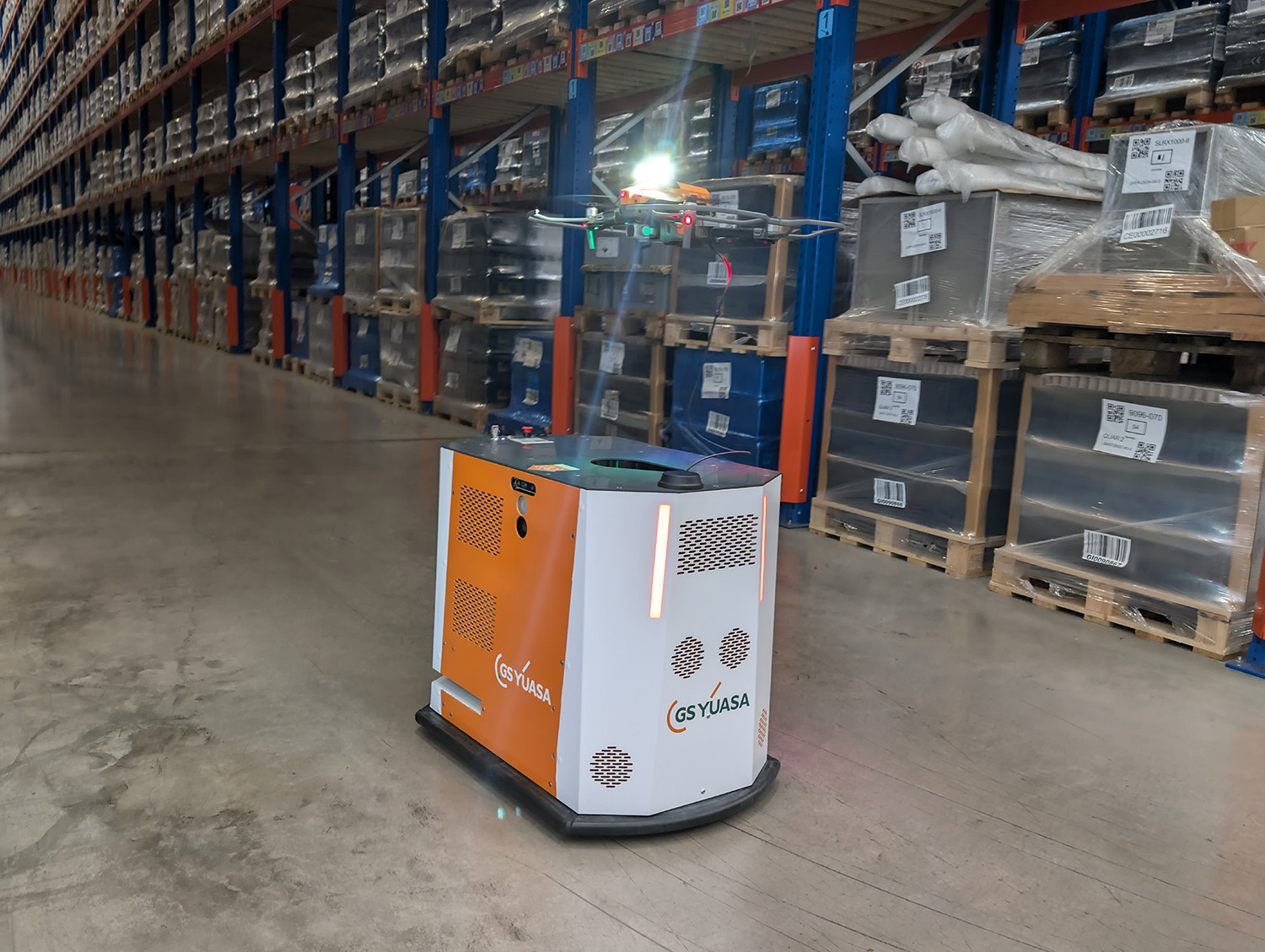
Looking Ahead
Following the success of this engagement, GS Yuasa will now embed inventAIRy XL into their routine inventory assurance processes. Rather than relying solely on a single annual count, the team’s vision is to cycle through all pallet locations periodically throughout the year, using their existing inventAIRy XL system to validate physical stock on an ongoing basis.
This continuous approach will ensure that the physical world– what’s actually in each rack location – remains consistently aligned with the virtual world recorded in their Warehouse Management System. By maintaining this level of data integrity, GS Yuasa will be able to act on exceptions faster, reduce stock discrepancies, and ensure continued confidence across their wider supply chain.
Client: GS Yuasa Battery Sales UK Ltd
Industry: Manufacturing / Distribution
Location: Ignition Park Distribution Centre, Swindon, UK
Solution: inventAIRy XL Autonomous Inventory Drone System (3 systems)
Date of Deployment: March 2025
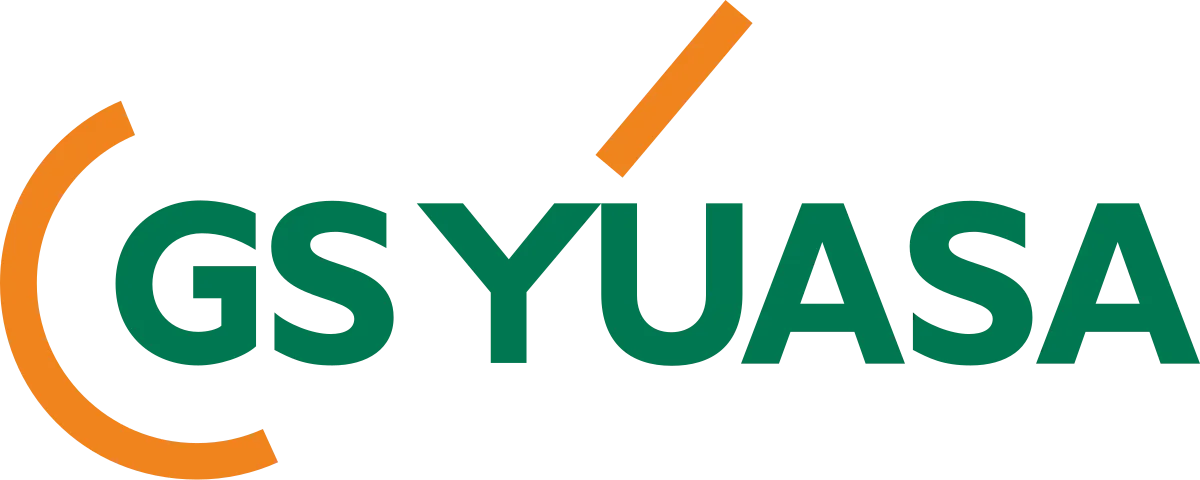
Overview
GS Yuasa is a globally recognised manufacturer of automotive and industrial batteries, with a long-standing reputation for engineering excellence and operational reliability. Their UK Distribution Centre in Swindon plays a pivotal role in the storage and distribution of batteries to customers across the UK and Europe.
Like many high-volume distribution centres, GS Yuasa places a premium on inventory accuracy – ensuring the right product is available at the right time. Historically, their approach to full wall-to-wall inventory audits, though rigorous, posed logistical and operational challenges. In 2024, GS Yuasa partnered with RAWview to deploy the inventAIRy XL solution – a cutting-edge autonomous drone system designed to perform high-density warehouse audits quickly, safely, and with minimal disruption.
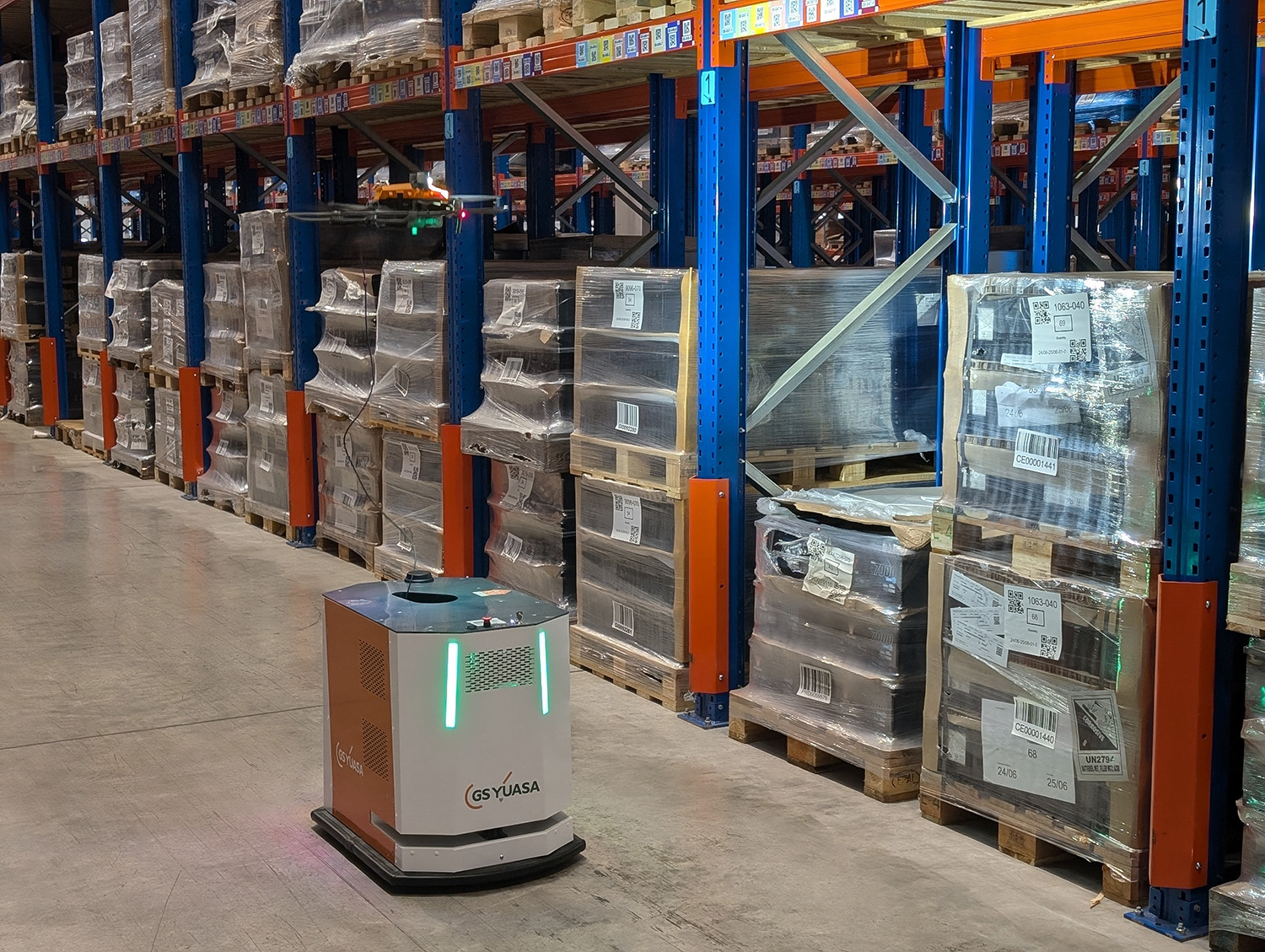
The Challenge
Prior to the introduction of inventAIRy XL, GS Yuasa’s annual inventory audit required a complete site shutdown for three days, during which all warehouse operations were paused. This approach came with a series of drawbacks:
- Significant downtime: A multi-day pause in operations affected inbound and outbound logistics, introducing bottlenecks and delays.
- High temporary labour demand: The audit required a large number of staff to work extended shifts, often on overtime rates, to ensure the task was completed on time.
- Equipment hire and safety concerns: Scissor lifts and manual barcode scanners were used to reach high-bay pallet locations, introducing safety risks and significant rental costs.
- Data lag: Inventory data could only be validated and reconciled once the audit was fully complete, delaying insights and corrective actions.
In short, the existing audit process was costly, disruptive, and resource-intensive.
The Solution: inventAIRy XL
To overcome these challenges, GS Yuasa implemented three inventAIRy XL systems across their Swindon facility.
inventAIRy XL is an autonomous inventory solution that combines a mobile robot, tethered drone, and AI-driven image capture system to automate stocktaking. It seamlessly navigates aisles, scans barcodes across all rack levels (including high bays), and automatically uploads inventory data to a secure user interface – eliminating the need for manual scanning and related equipment.
For GS Yuasa, the system was deployed to perform a full wall-to-wall audit of approximately 25,000 pallet locations, without interrupting their day-to-day operations.
The Outcome
The deployment proved to be a transformative success:
- Full audit completed in just 18 hours: The entire count was conducted overnight, with all three drones working in parallel to autonomously scan the warehouse – a fraction of the time previously required.
- Zero operational downtime: Unlike previous years, the audit required no site shutdown. Normal operations resumed immediately the following morning.
- Improved safety and reduced cost: The solution removed the need for temporary scissor-lift hire and greatly reduced the requirement for manual labour and overtime shifts.
- Real-time visibility: Inventory data was processed and available through the inventAIRy XL dashboard in real-time, giving GS Yuasa’s stock control team near-instant insights into their inventory accuracy.
- Scalable success: The use of three systems allowed for rapid coverage across all zones, demonstrating the potential to scale the approach to other sites or repeat the process more frequently.
Client Impact
This deployment marked a major shift in how GS Yuasa approaches inventory assurance. Not only did the inventAIRy XL solution deliver immediate operational efficiencies, but it also aligned with the company’s broader goals around digitisation, sustainability, and continuous improvement.
By reducing the need for powered access equipment, the audit also contributed to improved health and safety outcomes for staff and reduced emissions linked to equipment charging and extended operating hours.
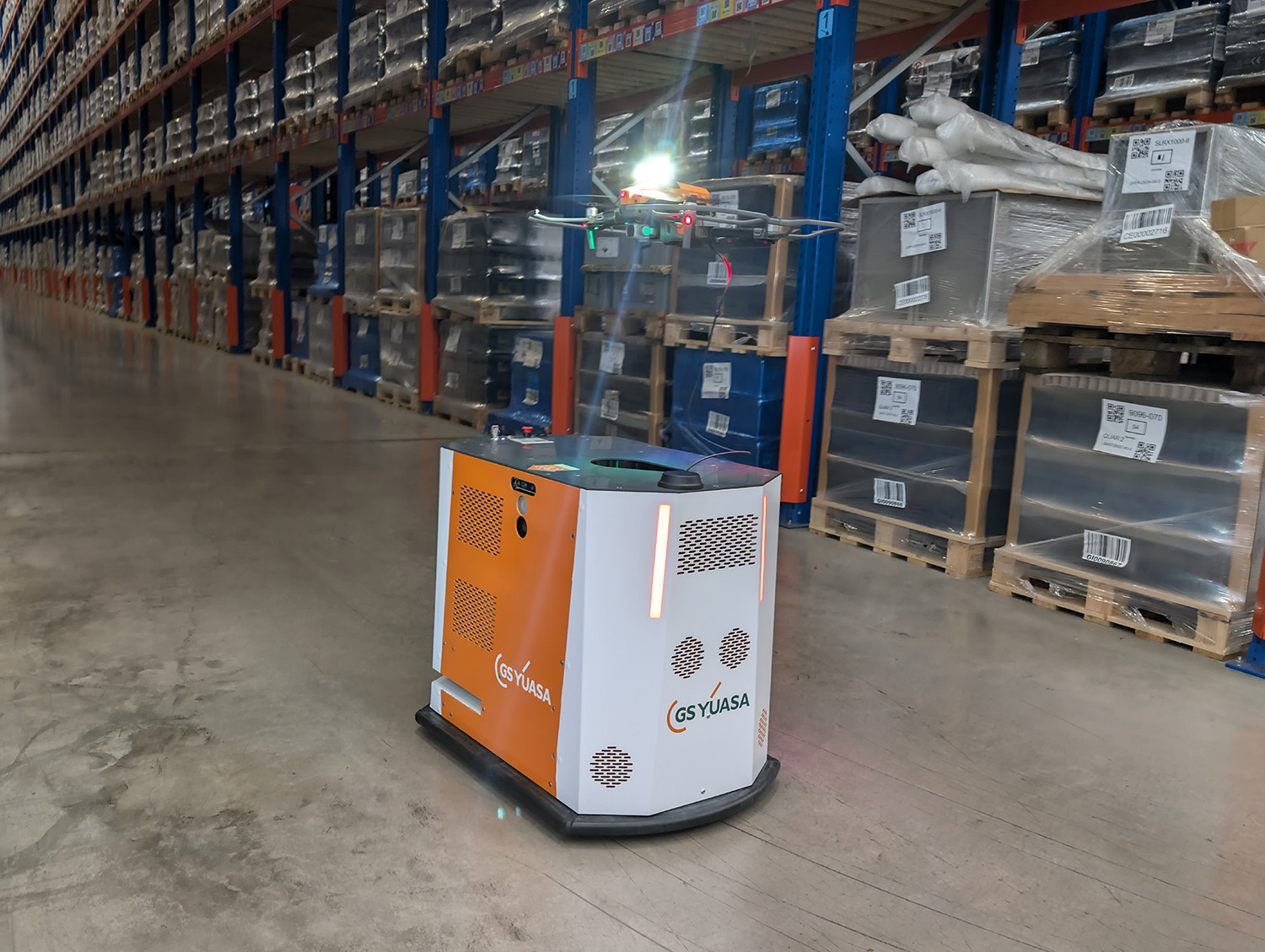
Looking Ahead
Following the success of this engagement, GS Yuasa will now embed inventAIRy XL into their routine inventory assurance processes. Rather than relying solely on a single annual count, the team’s vision is to cycle through all pallet locations periodically throughout the year, using their existing inventAIRy XL system to validate physical stock on an ongoing basis.
This continuous approach will ensure that the physical world– what’s actually in each rack location – remains consistently aligned with the virtual world recorded in their Warehouse Management System. By maintaining this level of data integrity, GS Yuasa will be able to act on exceptions faster, reduce stock discrepancies, and ensure continued confidence across their wider supply chain.
Client Testimonial
"We’ve been incredibly impressed with the performance and reliability of RAWview and of the inventAIRy XL solution. Since implementing it, our inventory management has become significantly more efficient and accurate. The system's reporting function is exceptionally easy to use and has saved our team countless hours of manual checking and helps to identify any misplaced stock. It’s clear that a lot of thought went into building a solution that truly understands the needs of modern inventory management.
The support team at RAWview have been responsive, diligent and knowledgeable every step of the way. Even when hiring in additional drones for our annual, year-end stock check, they were proactive and the service was second to none.
Thanks to RAWview, we’ve been able to streamline our operations, reduce human error, and improve customer satisfaction. We’d highly recommend to any business looking to upgrade their stock control processes"