What is the future of warehouse automation?
With tighter operating margins and growing consumer expectations, the cost of inefficiency soon adds up. For many logistics and operations teams, manual processes aren’t just slower, they’re holding the business back.
That’s why more companies are moving towards warehouse automation - not as a future initiative, but as a decisive step they can take right now. In this article, we break down the main drivers and show why now is the right time to make the change.
Where does the demand for warehouse automation come from?
Warehouse teams are under growing pressure to do more with less. That means: fewer people, tighter deadlines, and rising expectations around accuracy. Well, that’s where warehouse automation can support businesses.
In practice, warehouse automation simply means using technology to handle repetitive tasks like scanning inventory, updating records, or triggering alerts when things are not as expected. Instead of relying on staff to complete these steps manually, automated systems take care of them consistently and at scale.
The result is fewer mistakes, quicker turnaround times, and operations that can adapt as volumes change. For many, it's not solely about efficiency improvements, it's also about keeping up with the pace of modern logistics.
There are many benefits to adopting a warehouse automation strategy - some of the common ones:
- Improved efficiency: Warehouse automation reduces the time and effort required to complete tasks. This tends to lead to quicker turnaround times and improved productivity.
- Error reduction: Because tasks are now being completed by machines, the risk of human error is all but eliminated. In turn, this ensures better accuracy and consistency in the way tasks are carried out.
- Cost savings: By streamlining specific processes and reducing the need for manual labour, warehouse automation can lead to significant cost savings and fast payback periods.
- Scalability: Automated processes can easily adapt to changing workloads, making it easier for organisations to scale their operations.
- Better customer experience: When orders are accurate and issues are resolved quickly, consumers notice it. As we discussed at point 2, warehouse automation helps to reduce delays and errors, which means fewer complaints and a smoother experience.
How to identify a need for warehouse automation
If you're not sure whether it's time to invest in a warehouse automation strategy, here are some common signs to look for:
- Too much time spent on repetitive tasks: If your team is regularly tied up with routine activities like inventory scanning, data entry, or chasing misplaced stock, it's likely those hours could be better spent elsewhere. Warehouse automation helps free up your people for higher-value work.
- Business has scaled, but processes have been left behind: It goes without saying that growth is a good problem to have, but if you're handling more volume with the same processes and headcount as before, issues will inevitably appear. Warehouse automation allows you to handle more throughput without having to burden your payroll.
- Errors starting to occur: When accuracy starts to decline, and you see evidence of issues like missed picks, incorrect stock levels, or compliance gaps, it’s often a clear sign that manual processes are starting to fail. Warehouse automation brings a level of consistency and control that's very hard to replicate with people.
- Data overload: Most warehouses generate loads of operational data, but if it’s sitting in spreadsheets and not being used to improve decision-making, it's next to useless. Warehouse automation can help structure that data and provide the right insights without your team having to analyse vast amounts of data manually.
- Competitors seem to be moving faster: If you’re noticing that competitors are delivering faster, more reliably, or at lower cost, the chances are they’re already automating parts of their warehouse operation. Doing nothing will likely lead to you getting too far behind them to recover.
How to automate a warehouse
Once you've identified your need for automation, the next step is to make sure you implement it in a way that delivers real value. Here’s how you can approach that:
- Map out the problems you want to solve: Walk the warehouse and talk to the team. Understand where the real challenge is. Maybe it's that stock checks drag on too long or manual data entry creates errors. Try and make your initial focus on the "quick wins" that can make a visible difference to the operation.
- Select the right tools: There’s no shortage of warehouse automation tech out there, but not all of it is suitable for every warehouse. Whether it’s inventory drones, pick-to-light systems, or simple barcode process automation, look for solutions that will work with your current setup and won’t require a complete overhaul.
- Bring your team with you: Even the best warehouse automation strategies will fail if the people engaging with them don’t understand the bigger picture. Try and invest time in training and keep staff involved, as much as possible, throughout the implementation.
- Aim to continuously improve: Don’t try to aim for full transformation all at once. Trial the solution in a focused warehouse, measure the outcome, and refine before scaling across other warehouses. Warehouse automation works best when it’s treated as a Continuous Improvement project; not a one-off implementation.
- Quantify and track success: Whether it's time saved per inventory cycle, error rates, or reduced downtime, pick a handful of KPIs that actually reflect value to your business and your customers. Don't just track the metrics that are easy to measure.
- Adapt to change: As your operation evolves, so should your warehouse automation strategy. Advancements to the technology or changes in customer demand may mean the project needs a few subtle tweaks along the way. Position yourself and your technology integrator to be ready to adapt without starting again from scratch.
Conclusion
If your warehouse is running at or close to capacity, it’s probably time to take a serious look at a warehouse automation strategy. The signs are usually clear: too much manual work, too many errors, not enough time or people to keep up with demand.
The good news is that you don’t need to overhaul everything overnight. Start with the areas that cause the most friction, apply the right tools, and build things up from there. Warehouse automation isn’t about replacing people, it’s about giving your team the tools to work smarter and to help them keep up as things continue to scale.
In logistics, waiting too long to embrace automation will almost always cost your business more than actually taking the action to address the need. So if you're starting to identify at least some of the challenges we've explored in this article, now’s the time to take decisive action.
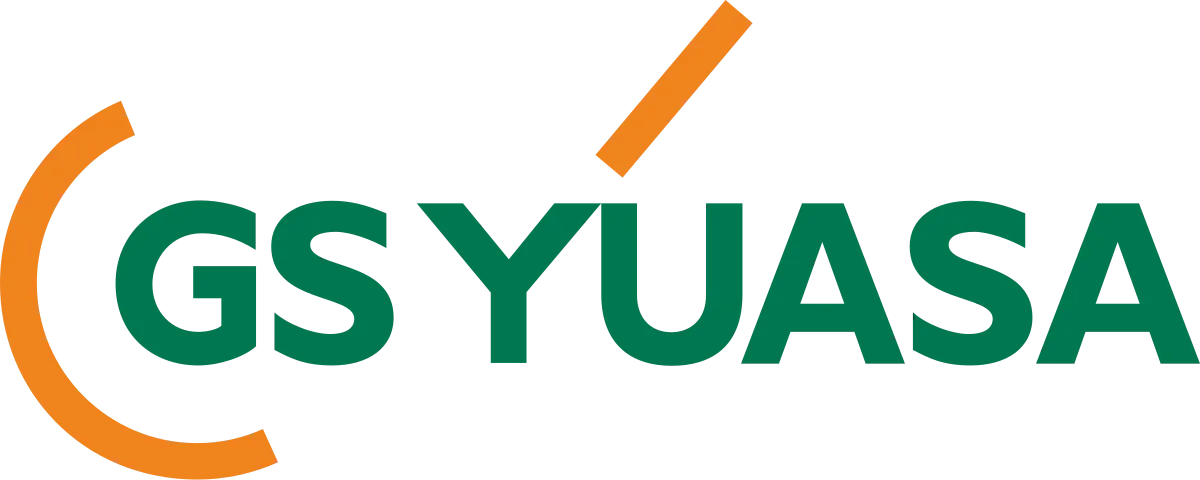
With tighter operating margins and growing consumer expectations, the cost of inefficiency soon adds up. For many logistics and operations teams, manual processes aren’t just slower, they’re holding the business back.
That’s why more companies are moving towards warehouse automation - not as a future initiative, but as a decisive step they can take right now. In this article, we break down the main drivers and show why now is the right time to make the change.
Where does the demand for warehouse automation come from?
Warehouse teams are under growing pressure to do more with less. That means: fewer people, tighter deadlines, and rising expectations around accuracy. Well, that’s where warehouse automation can support businesses.
In practice, warehouse automation simply means using technology to handle repetitive tasks like scanning inventory, updating records, or triggering alerts when things are not as expected. Instead of relying on staff to complete these steps manually, automated systems take care of them consistently and at scale.
The result is fewer mistakes, quicker turnaround times, and operations that can adapt as volumes change. For many, it's not solely about efficiency improvements, it's also about keeping up with the pace of modern logistics.
There are many benefits to adopting a warehouse automation strategy - some of the common ones:
- Improved efficiency: Warehouse automation reduces the time and effort required to complete tasks. This tends to lead to quicker turnaround times and improved productivity.
- Error reduction: Because tasks are now being completed by machines, the risk of human error is all but eliminated. In turn, this ensures better accuracy and consistency in the way tasks are carried out.
- Cost savings: By streamlining specific processes and reducing the need for manual labour, warehouse automation can lead to significant cost savings and fast payback periods.
- Scalability: Automated processes can easily adapt to changing workloads, making it easier for organisations to scale their operations.
- Better customer experience: When orders are accurate and issues are resolved quickly, consumers notice it. As we discussed at point 2, warehouse automation helps to reduce delays and errors, which means fewer complaints and a smoother experience.
How to identify a need for warehouse automation
If you're not sure whether it's time to invest in a warehouse automation strategy, here are some common signs to look for:
- Too much time spent on repetitive tasks: If your team is regularly tied up with routine activities like inventory scanning, data entry, or chasing misplaced stock, it's likely those hours could be better spent elsewhere. Warehouse automation helps free up your people for higher-value work.
- Business has scaled, but processes have been left behind: It goes without saying that growth is a good problem to have, but if you're handling more volume with the same processes and headcount as before, issues will inevitably appear. Warehouse automation allows you to handle more throughput without having to burden your payroll.
- Errors starting to occur: When accuracy starts to decline, and you see evidence of issues like missed picks, incorrect stock levels, or compliance gaps, it’s often a clear sign that manual processes are starting to fail. Warehouse automation brings a level of consistency and control that's very hard to replicate with people.
- Data overload: Most warehouses generate loads of operational data, but if it’s sitting in spreadsheets and not being used to improve decision-making, it's next to useless. Warehouse automation can help structure that data and provide the right insights without your team having to analyse vast amounts of data manually.
- Competitors seem to be moving faster: If you’re noticing that competitors are delivering faster, more reliably, or at lower cost, the chances are they’re already automating parts of their warehouse operation. Doing nothing will likely lead to you getting too far behind them to recover.
How to automate a warehouse
Once you've identified your need for automation, the next step is to make sure you implement it in a way that delivers real value. Here’s how you can approach that:
- Map out the problems you want to solve: Walk the warehouse and talk to the team. Understand where the real challenge is. Maybe it's that stock checks drag on too long or manual data entry creates errors. Try and make your initial focus on the "quick wins" that can make a visible difference to the operation.
- Select the right tools: There’s no shortage of warehouse automation tech out there, but not all of it is suitable for every warehouse. Whether it’s inventory drones, pick-to-light systems, or simple barcode process automation, look for solutions that will work with your current setup and won’t require a complete overhaul.
- Bring your team with you: Even the best warehouse automation strategies will fail if the people engaging with them don’t understand the bigger picture. Try and invest time in training and keep staff involved, as much as possible, throughout the implementation.
- Aim to continuously improve: Don’t try to aim for full transformation all at once. Trial the solution in a focused warehouse, measure the outcome, and refine before scaling across other warehouses. Warehouse automation works best when it’s treated as a Continuous Improvement project; not a one-off implementation.
- Quantify and track success: Whether it's time saved per inventory cycle, error rates, or reduced downtime, pick a handful of KPIs that actually reflect value to your business and your customers. Don't just track the metrics that are easy to measure.
- Adapt to change: As your operation evolves, so should your warehouse automation strategy. Advancements to the technology or changes in customer demand may mean the project needs a few subtle tweaks along the way. Position yourself and your technology integrator to be ready to adapt without starting again from scratch.
Conclusion
If your warehouse is running at or close to capacity, it’s probably time to take a serious look at a warehouse automation strategy. The signs are usually clear: too much manual work, too many errors, not enough time or people to keep up with demand.
The good news is that you don’t need to overhaul everything overnight. Start with the areas that cause the most friction, apply the right tools, and build things up from there. Warehouse automation isn’t about replacing people, it’s about giving your team the tools to work smarter and to help them keep up as things continue to scale.
In logistics, waiting too long to embrace automation will almost always cost your business more than actually taking the action to address the need. So if you're starting to identify at least some of the challenges we've explored in this article, now’s the time to take decisive action.