How does an autonomous mobile robot work?
Given that much of the technology that our solutions are centred around are based on Autonomous Mobile Robots (AMRs), we thought it high time to share some insights on how this intelligent technology actually works.
Autonomous Mobile Robots are intelligent machines that are designed to navigate and perform specific tasks in dynamic environments without direct human intervention. Whilst the technology itself is highly complex, we’ve created a simplified explanation below of how they work:
1. Perception
Sensors: AMRs are equipped with various sensors such as LiDAR (Light Detection and Ranging) scanners, cameras, ultrasonic sensors, and encoders. These sensors provide information about the robot’s surroundings, including obstacles (both static and dynamic), terrain, and landmarks.
Mapping: Using sensor data, the AMR is able to build a highly precise digital replica of its operating environment. This map helps the robot to understand its location relative to obstacles and to navigate efficiently and completely autonomously.
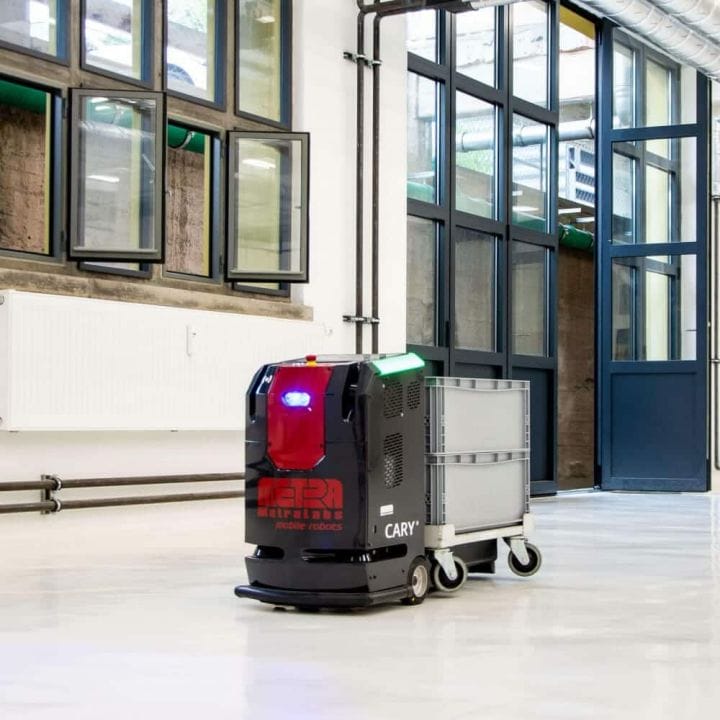
2. Localisation
Localisation algorithms use sensor data from the AMR and compares this with the map to determine the robot’s precise position within its environment. Techniques such as simultaneous localization and mapping (SLAM) enable the AMR to navigate accurately, even in unfamiliar or changing environments.
3. Path Planning
Once the robot knows its current location and its destination (or goal point), it uses intelligent path planning algorithms to determine the optimal route to reach the target while avoiding obstacles. These algorithms consider various factors such as distance, speed, and safety constraints like so-called “no-go zones”.
4. Motion Control
Motion control algorithms translate the planned path into commands that are sent to the AMR’s drive wheel motors, which are responsible for controlling the robot’s movement. These commands adjust the robot’s speed, direction, and acceleration to follow the desired path while maintaining stability and avoiding collisions.
5. Decision Making
AMRs often incorporate decision-making algorithms to handle dynamic situations or unexpected obstacles. These algorithms allow the robot to adapt its path plan or behaviour in real-time based on sensor feedback and predefined rules or objectives.
6. Task Execution
Once the robot reaches its destination, it performs the designated task, which could include transporting goods from a storage area to the production line (in the case of CARY), conducting an autonomous inventory audit in high-bay racking (in the case of inventAIRy XL) or scanning RFID tags in a retail store (in the case of TORY).
7. Safety Features
Such is their autonomous intent, safety features and failsafes are critical in any AMR application. As such, the robots will often include features such as collision detection and emergency stop mechanisms to prevent accidents and ensure the safety of both the robot and its surroundings. These features usually rely on sensors, the data from which is then interpreted and converted into a safety action by software algorithms.
To summarise, Autonomous Mobile Robots navigate and perform tasks using a combination of perception, localisation, path planning, motion control, decision-making, and safety features. By integrating these capabilities, AMRs can operate independently and in a diverse range of environments, from warehouses and factories to retail stores, revolutionising these industries and improving process efficiency and productivity.
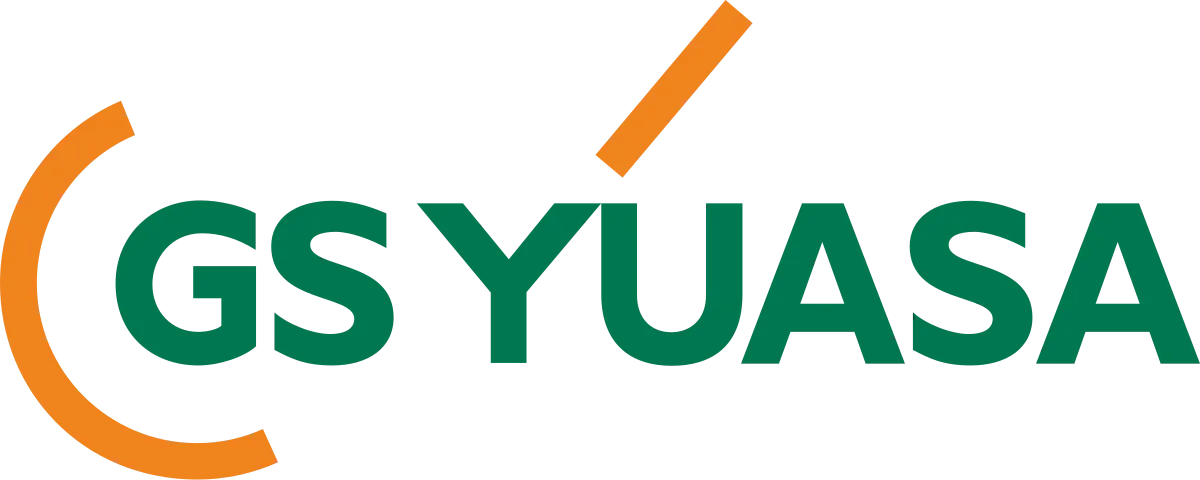
Given that much of the technology that our solutions are centred around are based on Autonomous Mobile Robots (AMRs), we thought it high time to share some insights on how this intelligent technology actually works.
Autonomous Mobile Robots are intelligent machines that are designed to navigate and perform specific tasks in dynamic environments without direct human intervention. Whilst the technology itself is highly complex, we’ve created a simplified explanation below of how they work:
1. Perception
Sensors: AMRs are equipped with various sensors such as LiDAR (Light Detection and Ranging) scanners, cameras, ultrasonic sensors, and encoders. These sensors provide information about the robot’s surroundings, including obstacles (both static and dynamic), terrain, and landmarks.
Mapping: Using sensor data, the AMR is able to build a highly precise digital replica of its operating environment. This map helps the robot to understand its location relative to obstacles and to navigate efficiently and completely autonomously.
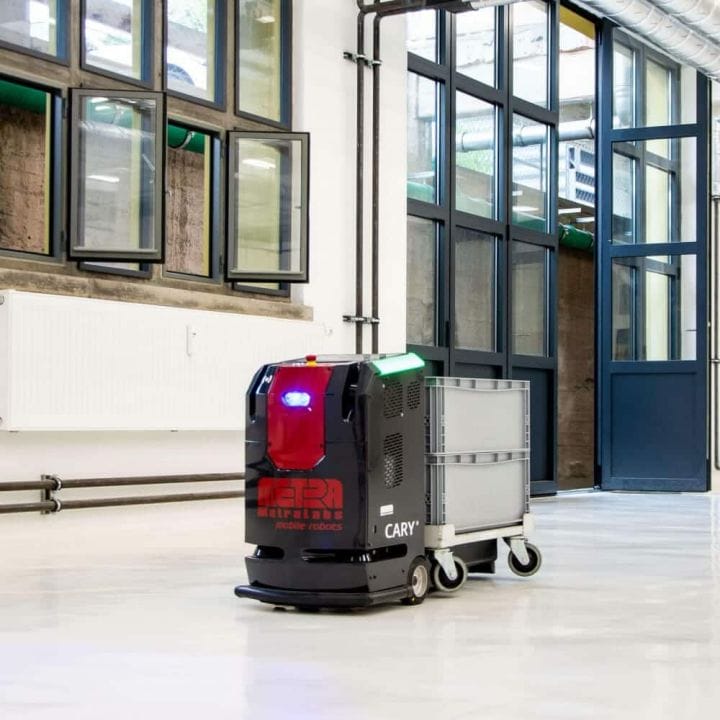
2. Localisation
Localisation algorithms use sensor data from the AMR and compares this with the map to determine the robot’s precise position within its environment. Techniques such as simultaneous localization and mapping (SLAM) enable the AMR to navigate accurately, even in unfamiliar or changing environments.
3. Path Planning
Once the robot knows its current location and its destination (or goal point), it uses intelligent path planning algorithms to determine the optimal route to reach the target while avoiding obstacles. These algorithms consider various factors such as distance, speed, and safety constraints like so-called “no-go zones”.
4. Motion Control
Motion control algorithms translate the planned path into commands that are sent to the AMR’s drive wheel motors, which are responsible for controlling the robot’s movement. These commands adjust the robot’s speed, direction, and acceleration to follow the desired path while maintaining stability and avoiding collisions.
5. Decision Making
AMRs often incorporate decision-making algorithms to handle dynamic situations or unexpected obstacles. These algorithms allow the robot to adapt its path plan or behaviour in real-time based on sensor feedback and predefined rules or objectives.
6. Task Execution
Once the robot reaches its destination, it performs the designated task, which could include transporting goods from a storage area to the production line (in the case of CARY), conducting an autonomous inventory audit in high-bay racking (in the case of inventAIRy XL) or scanning RFID tags in a retail store (in the case of TORY).
7. Safety Features
Such is their autonomous intent, safety features and failsafes are critical in any AMR application. As such, the robots will often include features such as collision detection and emergency stop mechanisms to prevent accidents and ensure the safety of both the robot and its surroundings. These features usually rely on sensors, the data from which is then interpreted and converted into a safety action by software algorithms.
To summarise, Autonomous Mobile Robots navigate and perform tasks using a combination of perception, localisation, path planning, motion control, decision-making, and safety features. By integrating these capabilities, AMRs can operate independently and in a diverse range of environments, from warehouses and factories to retail stores, revolutionising these industries and improving process efficiency and productivity.