Autonomous robots vs traditional warehouse drones
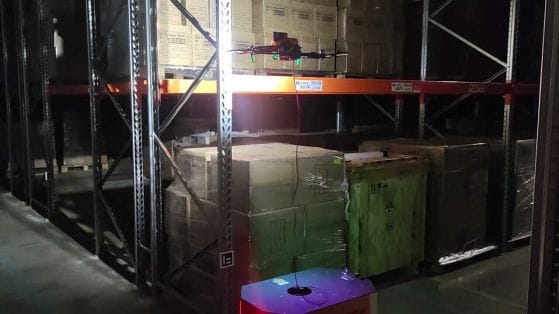
Drones have been growing in popularity in a range of industries in recent years; from aggregates and construction companies to security patrols and sports teams, more and more companies are streamlining their operations with clever use of drones.
Logistics could benefit hugely from automation, but traditional drones have struggled to find their way into warehouses due to some insurmountable issues.
The solution is here with AMR – autonomous mobile robots. These can be used for everything from stock picking (as seen in fulfilment centres like those used by Amazon) through to inventory management (as with inventAIRy XL).
But this is still a new technology and many of the clients we speak to tend to conflate the two rather than understand the key differences. This means they risk missing out on one of the most exciting developments in the industry or, as we have seen in some instances, opting for a drone solution that solves none of the traditional problems.
So what are the differences between the two technologies? It helps to first look at how inventory control drones work in a warehouse and why that’s not ideal – and then we can look at why an AMR is the better choice.
How do drones work?
In order to automate a drone’s journey, you typically need to set up a series of navigation waypoints. These map out the journey the drone needs to take to fulfill whichever task it’s performing. As an example from an established industry – aggregates – the waypoints guide the drone around the stockpile so it can calculate its volume.
Setting those up in an open space is straightforward (though time-consuming), but in a warehouse, that often requires substantial changes to the layout that is hugely disruptive to the business.
It also requires GPS tracking that, under a heavy warehouse roof, becomes unreliable. The other option is that the drone scans directional markers that have been placed around the warehouse – but this means the warehouse needs to be lit to perform its task, leading to an unnecessary waste of electricity.
Alternatively, as with use cases like assisting in football training, the drones would be operated by a person – which then means they not really automated, and doesn’t fully remove humans from the process. That would not be ideal in a warehouse either.
Battery life is an issue too – warehouses are big places with a lot of rack locations to scan, but the limited battery life on a drone allows for a fraction of those to be scanned in one mission. One issue we know warehouses face is the length of time manual inventory counts take – and drones don’t really solve that problem.
What’s different about an Autonomous Mobile Robot?
AMR is a broad term that covers a variety of technologies, but essentially they take AGVs (automatic guided vehicles – units capable of travelling along a pre-set path) to the next level by adding in greater flexibility and functionality. They are able to perform more tasks and, while they start with a mapped out route, are able to make adjustments to that where necessary.
One great analogy we saw was it’s the difference between a train and a taxi – one has its set path for taking from A to B and can’t deviate from that (and can only get you so close to your destination) while the other can respond in real-time to get you where you need to go.
In the case of inventAIRy XL, that extra functionality is the pairing with an attached drone for pallet scanning. This means you get all the benefits that a drone offers – such as the ability to work at height to scan the pallets – without the drawbacks.
Both the ground unit and the drone are powered by a 5hr battery in the ground unit, meaning missions can cover far more locations than a traditional drone – around 2000 locations at a time.
The ground unit is programmed with a digital map of the warehouse, meaning no changes are needed to the layout and no GPS is required – the system can be up and running within a few days, rather than over several weeks, with little to no interruption in your operation.
But don’t worry about the risk of accidents – the ground unit is fitted with several clever methods to detect unexpected obstacles. Your team can go about their day, and inventAIRy XL can go about its day.
That’s assuming you’re running the stock counts during the day, of course. One of things several of our customers love is the fact they can turn off the lights, shut up for the day and go home knowing that the unit – like the shoemaking elves from the old fairytale – will spring into action. The drone has a headlight which allows it to continue its mission in the dark, knowing the ground unit knows exactly where its going.
Hopefully that highlights the key differences between a drone and autonomous robots and why the latter is far better placed to solve your inventory challenges.
If you want to see how an AMR could solve your inventory count challenges, email us or give us a call on 0203 488 4071.
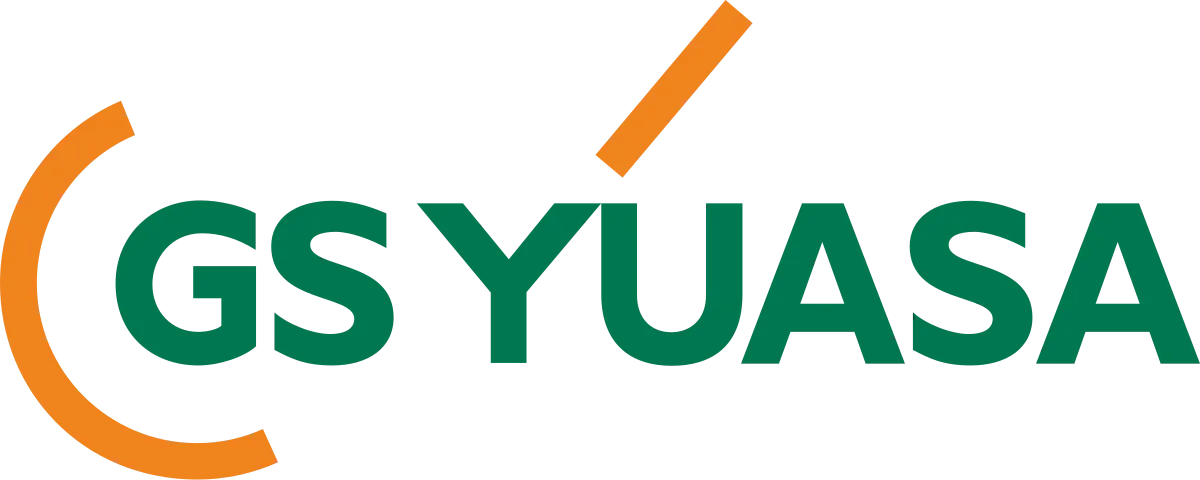
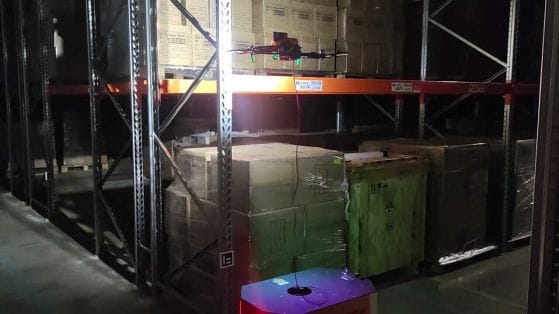
Drones have been growing in popularity in a range of industries in recent years; from aggregates and construction companies to security patrols and sports teams, more and more companies are streamlining their operations with clever use of drones.
Logistics could benefit hugely from automation, but traditional drones have struggled to find their way into warehouses due to some insurmountable issues.
The solution is here with AMR – autonomous mobile robots. These can be used for everything from stock picking (as seen in fulfilment centres like those used by Amazon) through to inventory management (as with inventAIRy XL).
But this is still a new technology and many of the clients we speak to tend to conflate the two rather than understand the key differences. This means they risk missing out on one of the most exciting developments in the industry or, as we have seen in some instances, opting for a drone solution that solves none of the traditional problems.
So what are the differences between the two technologies? It helps to first look at how inventory control drones work in a warehouse and why that’s not ideal – and then we can look at why an AMR is the better choice.
How do drones work?
In order to automate a drone’s journey, you typically need to set up a series of navigation waypoints. These map out the journey the drone needs to take to fulfill whichever task it’s performing. As an example from an established industry – aggregates – the waypoints guide the drone around the stockpile so it can calculate its volume.
Setting those up in an open space is straightforward (though time-consuming), but in a warehouse, that often requires substantial changes to the layout that is hugely disruptive to the business.
It also requires GPS tracking that, under a heavy warehouse roof, becomes unreliable. The other option is that the drone scans directional markers that have been placed around the warehouse – but this means the warehouse needs to be lit to perform its task, leading to an unnecessary waste of electricity.
Alternatively, as with use cases like assisting in football training, the drones would be operated by a person – which then means they not really automated, and doesn’t fully remove humans from the process. That would not be ideal in a warehouse either.
Battery life is an issue too – warehouses are big places with a lot of rack locations to scan, but the limited battery life on a drone allows for a fraction of those to be scanned in one mission. One issue we know warehouses face is the length of time manual inventory counts take – and drones don’t really solve that problem.
What’s different about an Autonomous Mobile Robot?
AMR is a broad term that covers a variety of technologies, but essentially they take AGVs (automatic guided vehicles – units capable of travelling along a pre-set path) to the next level by adding in greater flexibility and functionality. They are able to perform more tasks and, while they start with a mapped out route, are able to make adjustments to that where necessary.
One great analogy we saw was it’s the difference between a train and a taxi – one has its set path for taking from A to B and can’t deviate from that (and can only get you so close to your destination) while the other can respond in real-time to get you where you need to go.
In the case of inventAIRy XL, that extra functionality is the pairing with an attached drone for pallet scanning. This means you get all the benefits that a drone offers – such as the ability to work at height to scan the pallets – without the drawbacks.
Both the ground unit and the drone are powered by a 5hr battery in the ground unit, meaning missions can cover far more locations than a traditional drone – around 2000 locations at a time.
The ground unit is programmed with a digital map of the warehouse, meaning no changes are needed to the layout and no GPS is required – the system can be up and running within a few days, rather than over several weeks, with little to no interruption in your operation.
But don’t worry about the risk of accidents – the ground unit is fitted with several clever methods to detect unexpected obstacles. Your team can go about their day, and inventAIRy XL can go about its day.
That’s assuming you’re running the stock counts during the day, of course. One of things several of our customers love is the fact they can turn off the lights, shut up for the day and go home knowing that the unit – like the shoemaking elves from the old fairytale – will spring into action. The drone has a headlight which allows it to continue its mission in the dark, knowing the ground unit knows exactly where its going.
Hopefully that highlights the key differences between a drone and autonomous robots and why the latter is far better placed to solve your inventory challenges.
If you want to see how an AMR could solve your inventory count challenges, email us or give us a call on 0203 488 4071.